碳陶剎車盤∶電動智能化執行終端,藍海市場廣闊
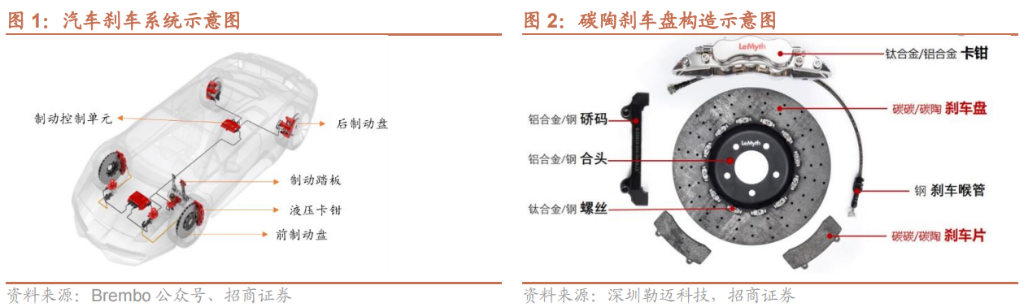
汽車和高速列車等現代交通工具的剎車材料經歷了從石棉材料、半金屬材料、粉末冶金材料到碳碳復合材料和碳陶復合材料的發展。
在各類剎車材料中,優良導熱性、穩定摩擦系數、耐高溫抗沖擊、耐磨減磨、質量輕便是制動閘片的重要發展方向,是搶占未來發展制高點的重點。
碳陶復合剎車材料是20世紀90年代發展起來的一種以高強度碳纖維為增強體,以熱解碳、碳化硅(SiC)等為基體的多相復合剎車材料,是在碳/碳復合剎車材料的基礎上,引入具有優異抗氧化性能的碳化硅(SiC)陶瓷硬質材料作為基體的一種剎車材料,既保持了碳/碳復合剎車材料密度低、耐高溫的優點,又克服了碳/碳剎車材料靜摩擦系數低、濕態衰減大、摩擦壽命不足及環境適應性差等缺點,成為新一代剎車材料,在汽車和高速列車等現代交通工具的剎車制動領域具有廣闊的應用前景。
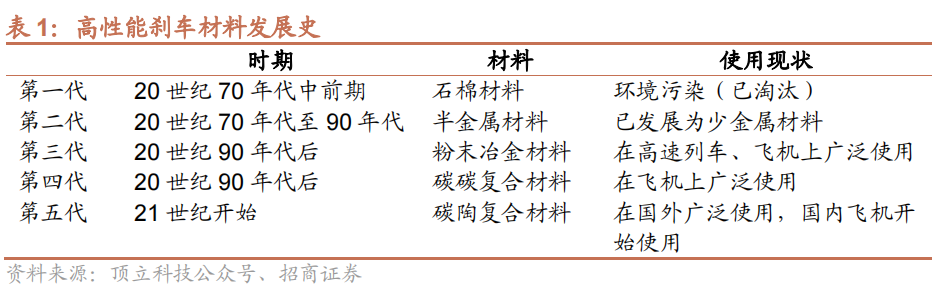
主流剎車材料主要有三類:金屬基剎車盤、碳碳材料剎車盤和碳陶剎車盤。目前廣泛用于高速列車、汽車和飛機上的剎車材料主要是粉末冶金和碳碳復合材料。
然而,粉末冶金剎車材料存在高溫容易粘結、摩擦性能易衰退、高溫強度下降顯著、抗熱震能力差、使用壽命短等缺點;而碳碳剎車材料存在靜態和濕態摩擦系數低(濕態相對干態衰減約50%)、熱庫體積大、生產周期長(約1200h)及生產成本高等問題,制約了其進一步發展及應用。
碳陶剎車盤結合了碳纖維和多晶碳化硅這兩者的物理特性。同時由于較輕的重量、良好的硬度、高壓和高溫條件下的穩定性、抗熱沖擊性和同韌性剪切斷裂特性等特點不但延長了剎車盤的使用壽命,并且避免了因負載而產生的所有問題。
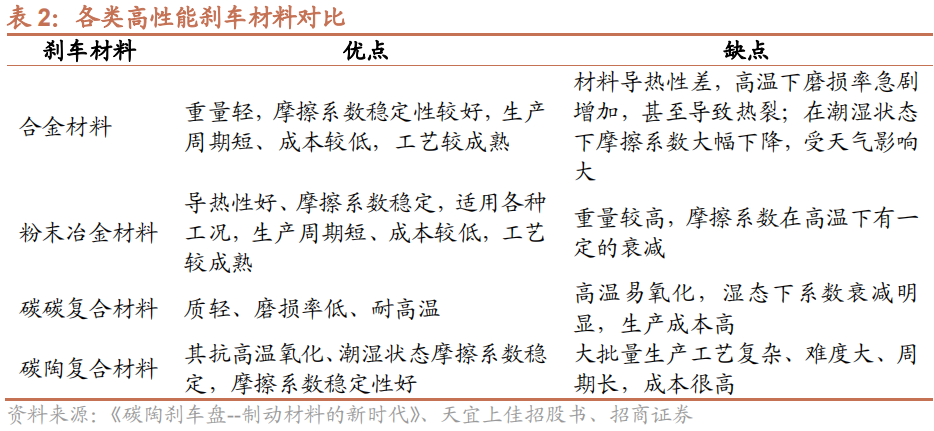
碳陶剎車盤性能明顯優于普通灰鑄鐵剎車盤,但成本為其短板。目前廣泛使用的制動盤材料主要有普通鑄鐵、低合金鑄鐵、普通鑄鋼、特殊合金鑄鋼、低合金鍛鋼及鑄鐵一鑄鋼(鍛鋼)復合材料等,鑄鐵材料的使用較為廣泛。
鑄鐵材料存在者制造周期長、導熱性差和易產生熱裂紋等不足,因此碳碳和碳陶復合材料為剎車材料的發展方向。
碳碳復合材料由于成本高,目前主要用于飛機制動器,隨著近年來高速鐵路的發展,國內外科技工作者開始研制開發用于高速鐵路的碳陶復合材料摩擦副,碳陶復合材料是一種國際上重點開發的摩擦副材料,我國也已經處于起步階段,碳陶剎車盤未來降本空間較大,有望成為剎車產品的主要發展方向。
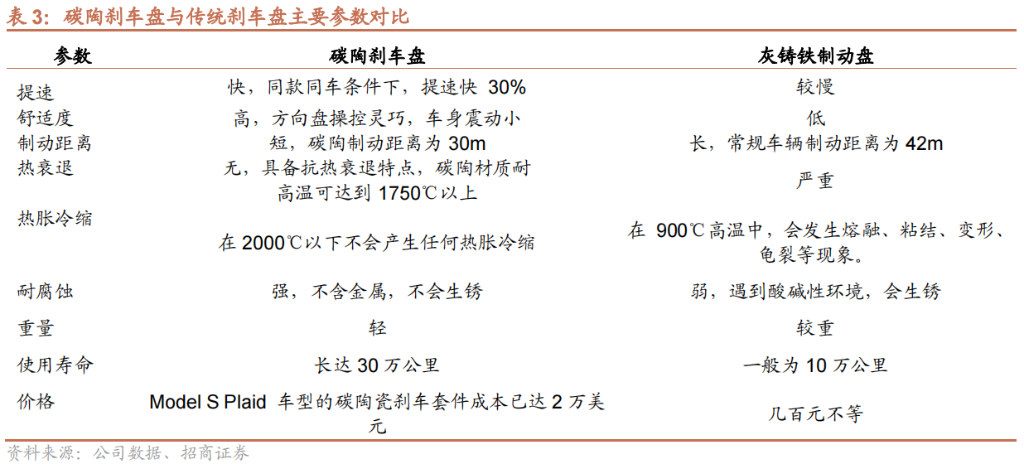
2、碳陶剎車盤優勢較為明顯,最早應用于豪華汽車
碳陶復合材料是由碳纖維的三維氈體或編織體作為增強骨架,碳與碳化硅陶瓷連續基體的一類新型復合材料。碳纖維的作用是提高材料的機械強度并為材料提供技術應用中所需的斷裂韌度,主要基體成分碳化硅決定著復合材料的硬度,陶瓷復合材料的同韌性剪切斷裂特性為其抗高熱負載和機械負載性能提供了保障。
因此,碳纖維增強碳化硅材料完美結合了碳纖維增強碳(C/C)和多晶碳化硅陶瓷這兩者的物理特性。碳陶復合材料的拉斷伸長率從0.1%~0.3%不等,這對于陶瓷材料而言是極高的數值。正因為具有這些特征,碳纖維增強碳化硅才成為高性能剎車制動系統的首選材料。尤其是較輕的重量、良好的硬度、高壓和高溫條件下的穩定性、抗熱沖擊性和同韌性剪切斷裂特性等特點延長了碳陶剎車片的使用壽命,并避免了傳統灰鑄鐵剎車片因負載而產生的所有問題。
碳陶剎車非常適合用于對剎車性能要求較高的交通工具,最早應用于超跑轎車。因為具有高溫穩定性、高導熱性、高比熱等特點,相對于鋼制剎車,碳陶剎車的優勢明顯:例如更長的使用壽命(長達30W公里)、更強的制動性能(耐高溫)、更輕的重量(同等尺寸下重量比傳統剎車碟要輕一半以上)等。
這種復合材料的剎車自1970年誕生代以來一直用于航空航天,最早應用于F16戰機,以減少在航母上降落的剎車熱衰退問題,后來十九世紀八十年代開始,碳陶剎車也在賽車項目中發展起來。
直到2001年,碳陶剎車才被用于量產民用上跑車,第一款采用了碳陶瓷剎車的量產車保時捷911 GT2,其在干濕路面的性能以及重量、舒適性、耐腐蝕性、使用壽命和賽道性能等方面都具有非常多的優勢。其他知名品牌汽車也陸續開始通過采用這一創新型剎車技術來提高車輛安全性并改善踏板舒適度,其中包括Mercedes-Benz的CL55AMG、奧迪W12&S8、賓利、布加迪和蘭博基尼等跑車與豪華汽車。
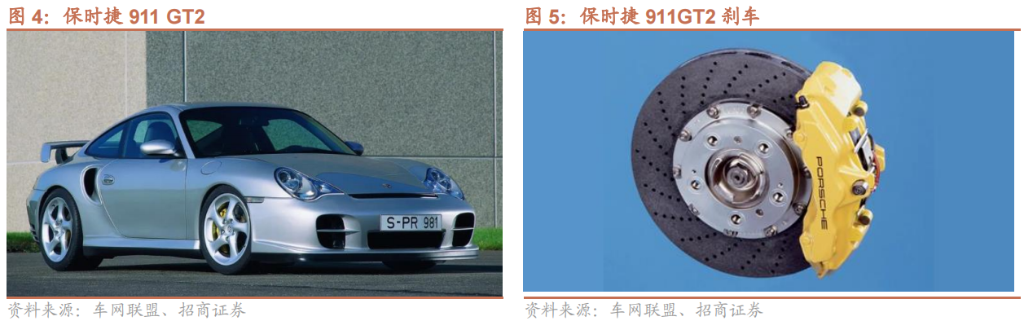

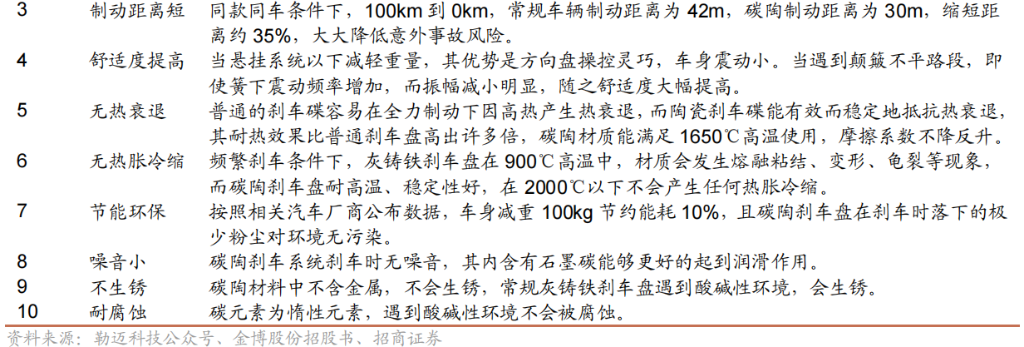
山東大學一研究團隊通過實驗來篩選最優的剎車盤和剎車片組合,通過實驗發現碳陶盤和碳陶剎車片、粉末冶金剎車片配副均顯示出較好的效果,其中,碳陶制動盤與碳陶剎車片組成的制動對偶,摩擦系數較高,摩擦磨損情況較其它組合好,碳陶材料作為汽車剎車副具有廣闊的發展前景。
在噪音方面,受制動器的制動結構影響,制動時有時出現摩擦聲音較大,而且后盤對偶摩擦系數偏高;前盤剎車片尺寸較大,盤與片的接觸面積大,制動較為平穩,摩擦系數適中,無制動噪聲。
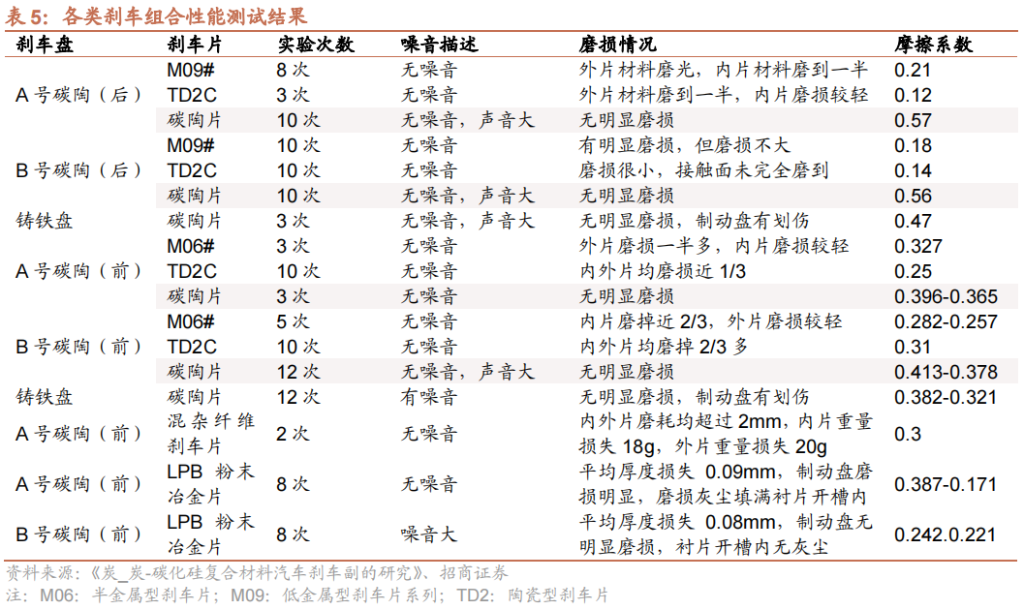
3、重要的智能化執行器件,符合電動車“增配、高配”趨勢
輕量化技術是未來汽車的重點發展方向。汽車零部件輕量化已經成為汽車節能減排最直接的解決方法之一。實驗證明,汽車整車重量降低10%,燃油效率可提高6%—8%;汽車整車質量每減少100公斤,百公里油耗可降低0.3—0.6升。此外,伴隨著新能源汽車的迅速普及,電動汽車對于續航里程的要求也更加迫切,在智能化網聯化的趨勢下,電動車增配了大量智能化設備,芯片、雷達、高清攝像頭以及數據傳輸的線束等,都給電動車的“體重”增加了不小的負擔,運用輕量化材料可以降低自身車重,在提升電動汽車性能的同時,實現節能減排。

電動化及輕量化趨勢下,碳陶盤能夠達到減重效果,降低里程焦慮。新能源車與燃油車相比,雖然沒有了發動機和變速箱,但是增加了電池組,重量相對于燃油車更重,因此新能源車減重任重道遠,碳陶剎車能有效降低懸掛系統以下重量,能更好的地適配新能源車,降低里程焦慮。
2021年11月,特斯拉宣布將在2022年中期,為旗下最快量產車ModelSPlaid車型提供碳陶瓷剎車套件,該套裝的成本已達2萬美元,約合人民幣12.78萬元。超高的車速,加上電車本身較大的質量,普通的制動系統在極限狀態下確實難堪重任,所以特斯拉準備給這款車換上尺寸更大的碳陶瓷剎車盤、鍛造的對向六活塞卡鉗以及高性能制動片,并且四個輪子均采用碳陶盤,以實現最強的制動效果。特斯拉表示:ModelSPlaid碳陶瓷剎車套件專為終極賽道體驗而設計,是一個完整的硬件套件,可在高性能駕駛期間提供最大、可重復的制動力。
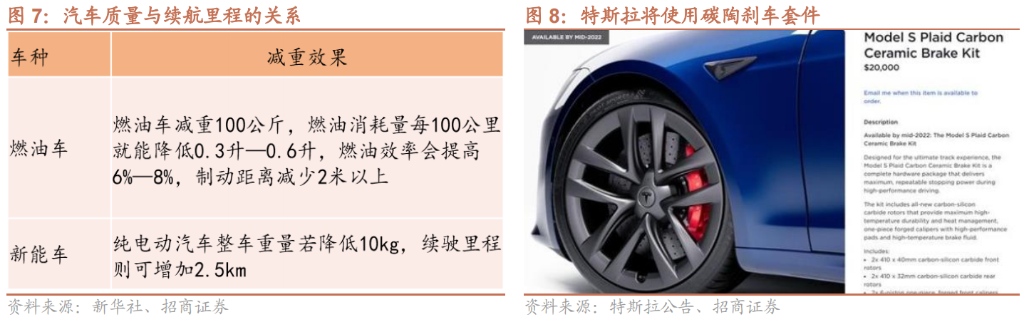
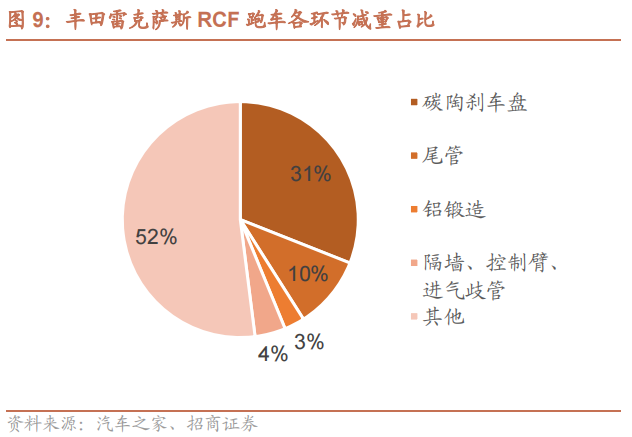
4、技術、規模降本空間大,成本下降曲線陡峭
目前階段,碳/陶復合材料在剎車制動領域大規模應用的主要障礙為生產成本較高、大批量生產工藝復雜、難度大、周期長等。隨著碳/陶復合材料制備技術的提升、規模效益的展現,預計碳/陶復合材料將在摩擦制動領域得到廣泛的應用。
乘用車碳陶制動盤依據碳纖維狀態可以分為兩大類,分別是短纖盤和長纖盤。短纖盤國外居多,比較有代表性的是布雷博和西格里的CCM盤和CCB盤,其中CCB盤摩擦表面有一層耐磨的陶瓷涂層。長纖盤國內外均有,國外目前最頂級長纖盤是布雷博和西格里CCM-R盤,可以滿足普通使用和賽道使用。國內長纖盤,包括兩種,一種是不帶耐磨涂層的C/C-SiC盤,另外一種是帶耐磨涂層的P-C/C-SiC盤。
短纖盤的制備工藝主要是分為混料、模壓成型、碳化、陶瓷化、去重裝配。它的優點是制備周期比較短,僅需要一個月。因為是模壓成型,所以原材料利用率非常高,綜合成本比較低。但缺點也比較明顯,即強度比較低,韌性比較差,在使用過程容易出現掉塊、斷裂和崩邊的風險。
長纖盤的制備首先是將連續碳纖維用針刺法做成碳纖維預制件,然后用化學氣相滲透法增碳做成碳碳多孔體,再通過熔融滲硅進行陶瓷化做成碳陶復合材料,最后經機加工成碳陶制動盤。特點是所制備出來的碳陶制動盤綜合性能很好,缺點是制備周期比較長,整個工藝下來長達2個月,成本較高。
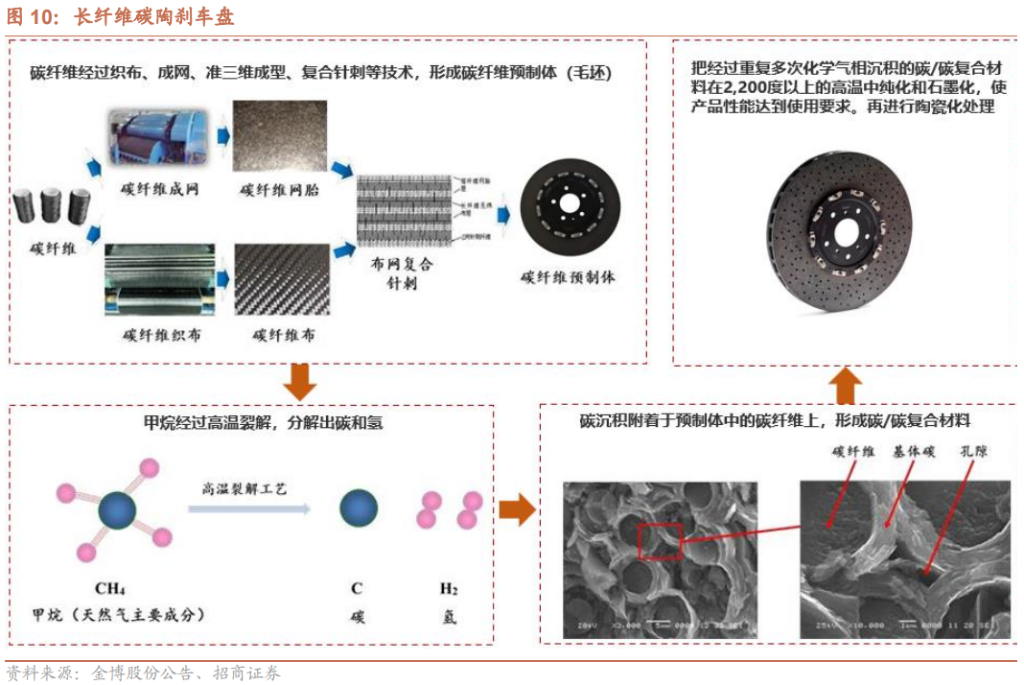
產品直接材料成本占比較低,存在較大技術、規模降本空間。以金博股份為例(公司全部產品系碳碳復合材料,成本結構代表性較強)。2021年公司熱場系列產品單噸成本為37萬元/噸,較2017年的46萬元/噸下降了20%,2021年單噸制造費用為11.40萬元,較2017年的24.68萬元下降了53.8%,技術降本顯著,2021年原材料成本占比為52%,隨著規模擴大、技術升級、自動化水平提升和碳纖維價格下降,產品的降本空間巨大。當前碳陶剎車片單片價格約2500-3500元,對用C級及以上乘用車市場,我們預計2025年單片價值有望下降到1000-1200元左右,將下探到B級及以上乘用車市場。
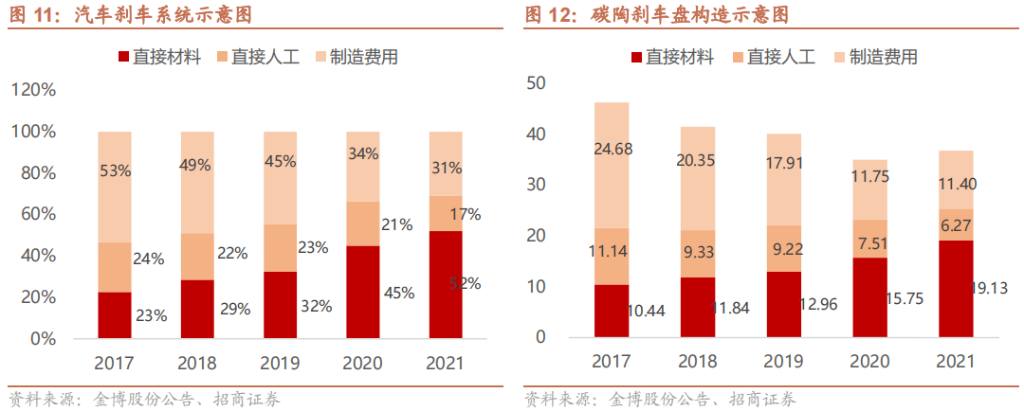
碳陶剎車盤未來市場空間大,增速高
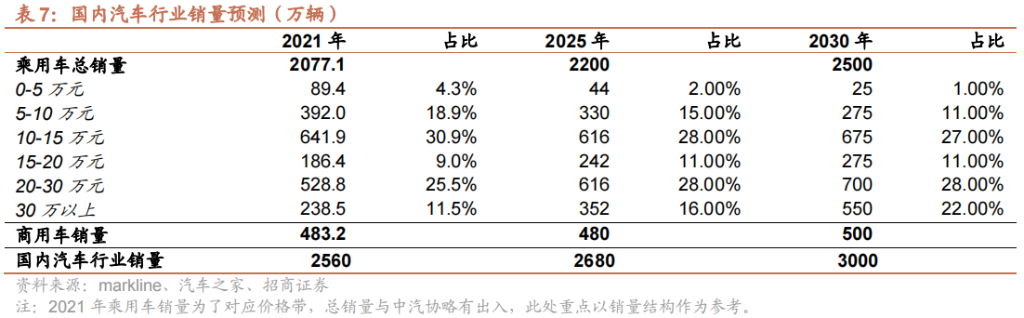
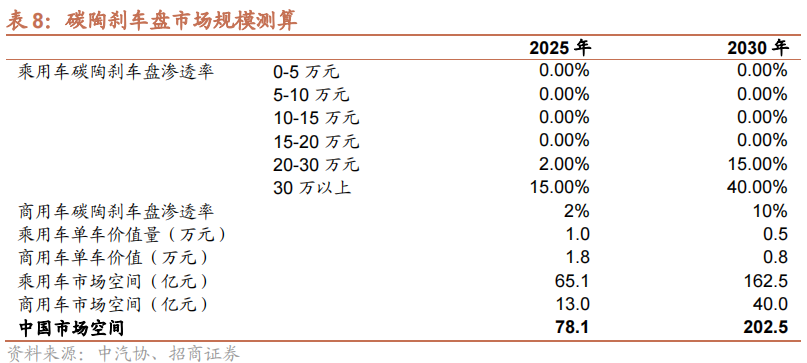
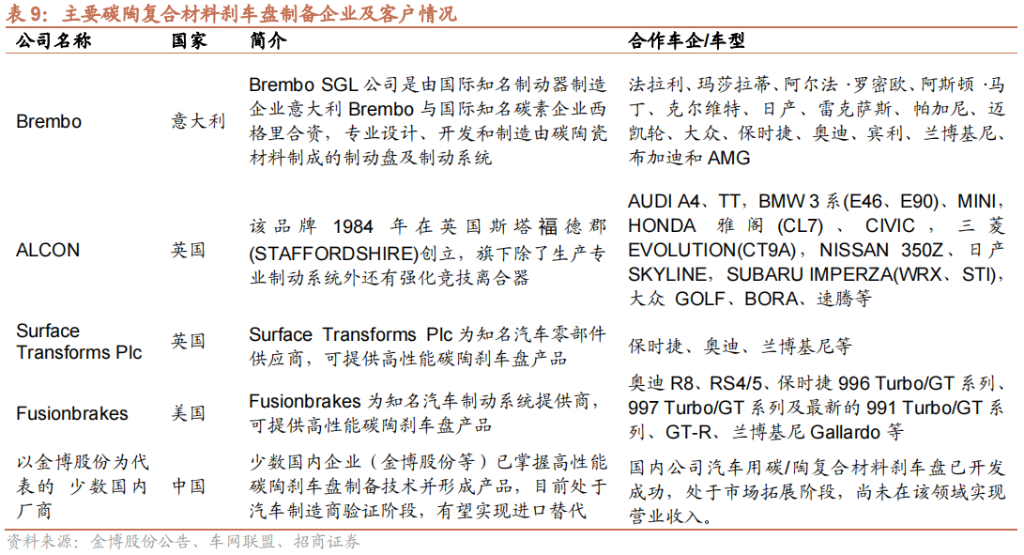
文章來源 | 招商證券
汪劉勝,楊獻宇